This week at The American Express, PGA TOUR star Rickie Fowler is advancing innovation in golf equipment with his custom lob wedge alteration.
While the majority of wedges—as well as golf clubs generally—are made via a combination of casting, forging, and milling techniques. Fowler uses 3D printing to create his novel 60-degree “RF” wedge, which is then precisely machined to his specification.
Since 2018, when it teamed up with metallurgy-focused Parmatech and printer manufacturer Hewlett Packard to start producing 3D-printed putters, Cobra Golf has been at the forefront of the 3D-printed golf club industry. To put it simply, CAD (computer-aided design) data are used by HP’s MetalJet 3D printer to create real club heads from powdered metal. The aim of Cobra is to produce clubs that are more accurate to the original designs and, ideally, more durable by using 3D printing as an alternative to forging or casting.
In addition to releasing retail lines of 3D-printed putters, like as the King 3D-printed putter series, Cobra has also experimented with irons and woods since 2018.
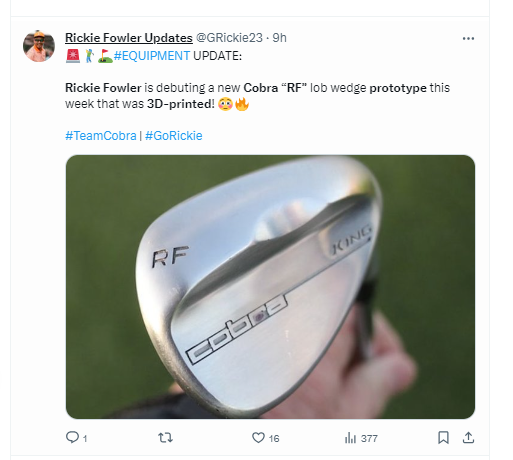
Fowler is now launching a brand-new, 3D-printed lob wedge this week at The American Express, which is tailored precisely to his tastes.
Fowler’s new 3D wedge design process began approximately six months ago, when he was looking to replace the sole/bounce structure on his old Cobra King lob wedge, according to Ben Schomin, Tour Operations Manager at Cobra.
“He was probably adjusting his one and only shape for almost half a year. The strong grind lines he used to apply have softened a great deal and have continued to do so. You can see and measure lines more easily if they are firm. It is now simpler to reproduce and recreate thanks to 3D printing. He was getting more camber out of his wedge grind, so at some point he thought, “Let’s just 3D scan it and print it, so it’s perfect.” Schomin told reporters on Tuesday at The American Express.
Rounder wedges with more camber can be used on full shots and from a variety of lies around the greens to assist the club move through the turf more readily rather than digging. Therefore, Cobra 3D scanned the prototype wedge to produce 3D-printed duplicate versions, one of which is in Fowler’s backpack this week in the desert, after fine-tuning the wedge head prototype to a point where Fowler was satisfied and at ease.
Since Fowler’s new lob wedge is now precisely tailored to his preferences, Cobra will be able to supply Fowler with duplicate wedges whenever needed. The new wedges should theoretically match the wedge design that Fowler and Schomin already designed.
In contrast to his peers on the PGA TOUR, Fowler doesn’t switch out his lob wedge too much. According to Schomin, Fowler likes a wedge that is a little bit more worn in to assist reduce the momentarily additional spin found in entirely new grooves. Nevertheless, Fowler replaces his lob wedge around every two months. When the time comes to replace this specific wedge, he will have a backup that is CNC-milled and 3D-printed to match the one he has in his bag this week.
Now that he has the ideal lob wedge, Fowler is driving innovation at Cobra and in the golf equipment industry as a whole.